The Chameleon pedestrian bridge would link
Soldier Field to Northery Island. But, will it stand? In this blog, I will apply basic structural principles and equations to estimate the material requirements of such a bridge. To the greatest extent possible, I have tried to remain true to the original design intent, but early schematic evaluations require lots of approximation.
My first caveat is that I’m a building engineer. The layman would be surprised at the differences between the thought processes and
building codes that apply to bridges and buildings. However, given the functional intent of this pedestrian bridge, it might is some senses be better treated as a building. To that end, I’ve used the Chicago Building Code (CBC) as a baseline for determining load conditions and general requirements. As we proceed, though, you may find that more elements of common vehicle bridges will find their way into the concept by way of seeking the most efficient forms.
As a building engineer, my first inclination was to evaluate the bridge concept as a beam. In the classic, simply supported beam, the greatest bulk of the structure would necessarily need to be located in the center of the span. However, the architectural intent is to minimize the mass of the structure where it most influences the efficiency of the design. That runs counter to the simple approach. Instead, I thought of the bridge as a system of two cantilevering beams. This type of layout places the greatest
cross-section size over the abutments.
Cantilever bridges were once very common, owing to the ability to construct out from the piers until meeting in the middle. This reduced or eliminated the need for temporary piers or barges located in the deepest part of the body of water below. Employing such a construction method would be advantageous in this example as well, so that the marina below could remain in operation to the fullest extent possible.
Before I could run some preliminary numbers, I needed to make several estimates about the size and scope of the project. From
Google maps, I estimated a free span of 600 ft. Taking all of the abutment requirements into account the real span might be a fair distance larger, but this estimate provides a baseline for exploring the concepts. Secondly, I estimated from the architectural sections, the dimensions of the superstructure. The platforms looked to be about 25 ft wide. The total height might be 45 ft. at the maximum depth. Since the exterior shape was to be comprised of many jagged surfaces, I applied a 33% reduction of the height to approximate the relative location of the main structural elements, treated as two lumps of steel - one representing the top chord of a
truss, and the other the bottom chord.
I could estimate the weight of the bridge by taking the lumped mass of steel plus another 50% to account for connections, web members and cladding. Depending on the type of façade and the interior build-out, that number could be substantially larger. For the live load, due to pedestrians and amenities, I applied the 100 PSF load stipulated by the CBC for corridors, lobbies and other public space. Notably missing from my quick calculations were allowances for the effects of mother nature. Snow accumulation and lateral wind pressures would place a particularly large demand on any actual structure.
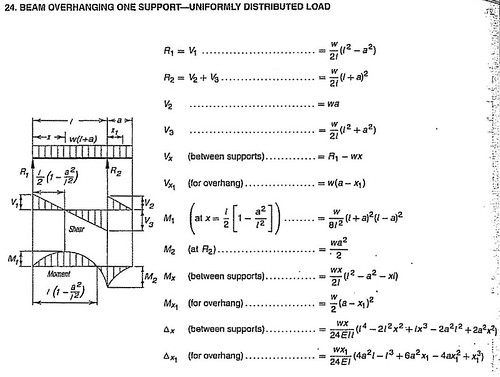
Nevertheless, I proceeded with a basic cantilever model. With the inputs described above, I was able to use pre-derived equations (taken from the AISC Steel Manual) to estimate the deflection of the beam at it’s cantilevered end and the amount of moment accumulated above the piers. As expected for such a long span, the deflections were large. Use of the spreadsheet allowed me to incrementally increase the amount of
structural steel until arriving at quantity that seemed to meet the criteria. Again using my building background, I sought a deflection of no more than the length of the span divided by 360 (an arbitrary, but typically justifiable criteria). A deflection due to live loads up to 20 in. would be acceptable.
I also experimented with the length of the back-span. Intuitively, I figured that the longer the back-span, the smaller the end displacements. However, since my simple equation assumed the same stiffness throughout the length of the beam, when the back-span length increased too much, it became too flexible to provide a steady prop for the cantilever. This suggests that the architectural concept, which shows a short but deep section behind the forward pier, conceptually meets the structural demand.
After iterating through my calculations to meet deflection and strength criteria, I arrived at a design that called for about 1200 tons of structural steel. In more graphic terms, the bridge truss superstructure would consist of thirteen 14 in. wide flange beams (I-shaped) each weighing about 120 pounds per foot. Considering the other factors left out of my analysis, this seemed like an expensive brute force way to achieve the design.
I thought back to the original intent to minimize structural mass where not required by strength demands. The simple model assumed that the entire length of the bridge consisted of the same size section. However, because we chose a cantilevered design, the forces in the members would decrease as we approached the end of the cantilever. The structural shape could also taper with that demand. I used RISA 2D, a simple
finite element analysis program, to compare the effect of tapered versus constant sections. In the tapered model, I reduced the weight of the section by 60% from the pier to the free end. As a baseline to see if I was still meeting the strength and stiffness minimums, I computed the deflection due to a constant live load first. The results showed an almost negligible difference. The effect on the
dead load deflection, however, was a significant 50% reduction.
These results indicated that the original design had been conceived with sound structural principles in mind. Of course, many issues still remain to be addressed. One such concern is whether the multi-faceted shell will be stable. The jagged exterior form seems to call for some type of internal space frame or self-bracing mechanism to prevent the perimeter from buckling. Surely solutions exist, but a what cost to the overall project.
Without even addressing many additional design considerations, the steel quantities that I had arrived at still seemed heavy. Perhaps more efficiencies could be realized without compromising the architecture. Looking for inspiration, I would turn to other bridge examples. In the form of
suspension bridges, I remembered the principles of catenary structures. To be continued in the next post…
How would you have conducted this schematic evaluation? Do you agree with the load applied? Would you have used the full section depth to estimate the building stiffness? What other important considerations were ignored in this evaluation?
![Reblog this post [with Zemanta]](http://img.zemanta.com/reblog_e.png?x-id=24742821-c520-4b18-adf6-73e82a57eca4)